SEMICONDUCTOR
MICROELECTRONICS & FIBER OPTIC
Our inspection and testing services assure that high purity gas cabinets, panels, filter skids, gas sticks, components, tool systems, laterals, or mains are fabricated and installed in accordance with project specifications and tested to the required performance criteria for leak rate, particle, and impurity concentration.
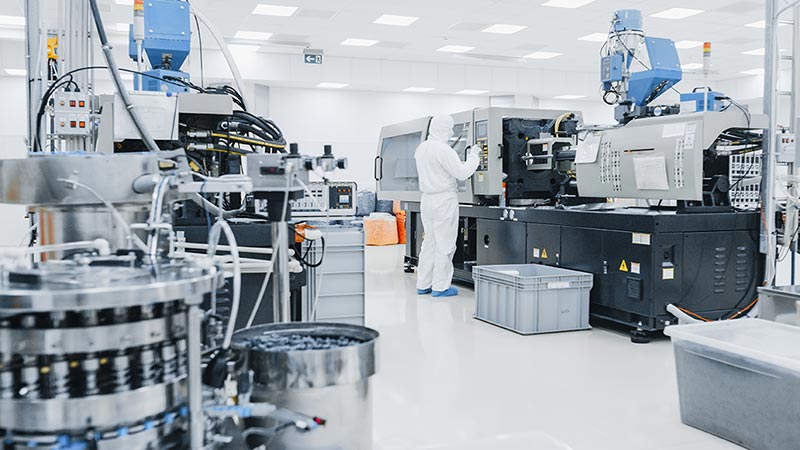
MICROELECTRONICS & FIBER OPTIC
Our inspection and testing services assure that high purity gas cabinets, panels, filter skids, gas sticks, components, tool systems, laterals, or mains are fabricated and installed in accordance with project specifications and tested to the required performance criteria for leak rate, particle, and impurity concentration.
TESTING
Inboard Helium Leak Testing / Mass Spectrometer Leak Testing (MSLT)
Outboard Helium Leak Testing / Mass Spectrometer Leak Testing (MSLT)
Particle Testing
Moisture and Oxygen Testing
impurity testing
Resources
STAFF
Our management team and technicians have the industry experience to perform any high purity testing scope of work. Troubleshooting techniques along with proven procedures, equipment resources, data acquisition, and electronic reporting capabilities provide the highest level of certification testing for process tool qualification, system, or equipment commissioning.
equipment
MS-Leak and analytical testing equipment is maintained by our full time Equipment Manager ensuring equipment is operating to OEM specifications and is calibrated in accordance with our Quality System and manufacturer’s recommendations
FABRICATION & INSTALLATION SURVEILLANCE
MATERIALS OF CONSTRUCTION
WELDING procedure specification
Welding Operator Performance Qualification
Auto-GTAW process WOPQ is evaluated for conformance to ASME Section IX and project specific qualification testing requirements.
purge & welding backing gas
Welding Surveillance
PVDF, PP, and PFA Welding
Welding machine and welder qualifications are verified to the requirements of the manufacturer. Weld machine parameters are verified on a weld for weld basis as part of the weld inspection process.
WELDING INSPECTION & SYSTEM VERIFICATION
Weld Inspection (SS, PVDF, PP, PFA)
Installation Verification (IV)
Final inspection of the system is a critical construction process. Systems are inspected for routing, hangers, labels, source, and POC tie-in per drawings. The IV process produces a punch or task list requiring corrective action and re-inspection or verification before sign off.